Los autómatas programables (PLCs) son el núcleo de la automatización industrial moderna, permitiendo el control preciso y fiable de procesos en diversas industrias. Entender las partes que componen un PLC no solo es esencial para su programación y mantenimiento, sino que también ayuda a comprender cómo funcionan y qué los hace tan versátiles.
En este artículo, exploraremos en profundidad cada uno de los componentes clave de un PLC, su función y cómo trabajan juntos para automatizar procesos industriales. ¡Prepárate para un recorrido por el corazón de la automatización!
La estructura general de un PLC
Antes de entrar en detalle, es importante entender cómo se organiza físicamente un PLC. Se componen de un chasis o rack que alberga módulos individuales, cada uno con funciones específicas. Los componentes principales son:
- CPU (Unidad Central de Procesamiento)
- Memoria
- Módulos de Entrada/Salida (E/S)
- Fuente de Alimentación
- Bus de Comunicación
- Interfaces de Comunicación
- Unidad de Programación
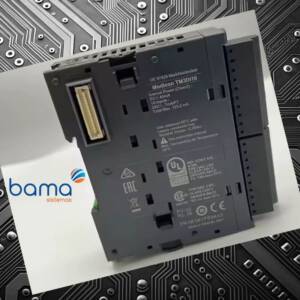
Memoria: almacenamiento y gestión de datos
La memoria es un componente fundamental de un autómata programable. Almacena el programa que define su comportamiento y registra los datos necesarios para la ejecución de los procesos.
Funciones principales:
- Guardar el programa que dicta cómo debe actuar el PLC.
- Registrar datos temporales durante el procesamiento, como estados de entradas y salidas.
- Conservar configuraciones críticas en memorias no volátiles.
Tipos de memoria:
- ROM (Read Only Memory): Contiene el sistema operativo y rutinas esenciales.
- RAM (Random Access Memory): Almacena datos temporales y el programa en ejecución.
- Memoria no volátil (NVRAM): Retiene los datos almacenados incluso sin alimentación eléctrica.
Módulos de Entrada/Salida (E/S): la conexión con el mundo exterior
Los módulos de entrada y salida son las interfaces entre el PLC y los dispositivos externos, permitiendo que el sistema interactúe con su entorno.
Entradas:
- Reciben señales de sensores, interruptores y dispositivos similares.
- Ejemplo: Un sensor de proximidad detecta la presencia de un objeto y envía la señal al PLC.
Salidas:
- Generan señales para controlar dispositivos como motores, válvulas o relés.
- Ejemplo: Activar un actuador para mover un brazo robótico.
Tipos de módulos:
- Digitales: Procesan señales de encendido/apagado.
- Analógicos: Manejan variables continuas, como temperatura o presión.
Fuente de alimentación: energía para el PLC
La fuente de alimentación proporciona la energía necesaria para que el PLC y sus módulos funcionen correctamente.
Funciones principales:
- Proveer voltaje y corriente adecuados para la CPU, los módulos de E/S y otros componentes.
- Proteger el sistema contra picos de tensión y fluctuaciones eléctricas.
Tipos de fuentes de alimentación:
- 24V DC: Común en aplicaciones industriales.
- 230V AC: Utilizada en sistemas conectados a redes eléctricas.
Bus de comunicación: la carretera de datos interna
El bus de comunicación es un sistema de líneas eléctricas y protocolos que permite la transferencia de datos y señales de control entre los diferentes módulos y componentes del PLC. Es esencial para garantizar que la CPU, la memoria y los módulos de entrada/salida trabajen en sincronía.
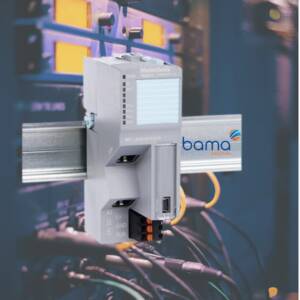
Tipos de buses de comunicación
Buses internos:
- Conectan los módulos dentro del PLC, como la CPU, la memoria y los módulos de E/S.
- Su diseño se enfoca en la velocidad y fiabilidad para operaciones internas.
Buses externos:
- Permiten la comunicación entre el PLC y otros dispositivos externos, como sensores, actuadores, o incluso otros PLCs.
- Diseñados para soportar largas distancias y manejar múltiples dispositivos en una red.
Normas y protocolos comunes
Los buses de comunicación están regulados por normas internacionales para garantizar compatibilidad, interoperabilidad y fiabilidad. Aquí tienes los más utilizados:
Modbus
Descripción: Uno de los protocolos más extendidos, diseñado para la comunicación entre dispositivos industriales.
Modos de funcionamiento:
- RTU (Remote Terminal Unit): Comunicación binaria compacta.
- ASCII: Comunicación más legible, pero menos eficiente.
Ventajas: Sencillez, coste bajo, ampliamente soportado.
Aplicaciones: Lectura de sensores, control de dispositivos básicos.
Profinet
Descripción: Protocolo basado en Ethernet diseñado para redes industriales.
Norma asociada: IEC 61158.
Características clave:
- Alta velocidad y capacidad para manejar grandes volúmenes de datos.
- Comunicación en tiempo real, crítica para aplicaciones como robótica.
Ventajas: Robustez, flexibilidad, integración con dispositivos avanzados.
Aplicaciones: Automoción, líneas de producción complejas.
Ethernet/IP
Descripción: Extensión del protocolo Ethernet para aplicaciones industriales.
Norma asociada: CIP (Common Industrial Protocol).
Características clave:
- Soporta grandes redes y múltiples dispositivos simultáneamente.
- Compatible con dispositivos industriales y de oficina.
Ventajas: Escalabilidad, compatibilidad con sistemas de TI.
Aplicaciones: Sistemas SCADA, automatización de grandes plantas.
CAN (Controller Area Network)
Descripción: Protocolo diseñado para entornos donde la comunicación en tiempo real es crucial.
Norma asociada: ISO 11898.
Características clave:
- Alta fiabilidad en entornos ruidosos.
- Uso eficiente del ancho de banda.
Ventajas: Robustez, comunicación distribuida.
Aplicaciones: Automoción, maquinaria agrícola.
Profibus
Descripción: Protocolo de comunicación en redes industriales, precursor de Profinet.
Norma asociada: IEC 61158.
Características clave:
- Comunicación eficiente entre múltiples dispositivos.
- Disponible en variantes para datos estándar (Profibus-DP) y procesos (Profibus-PA).
Ventajas: Fiabilidad, soporte amplio.
Aplicaciones: Industria química, control de procesos.
Diferencias clave entre buses
Protocolo | Velocidad | Distancia máxima | Aplicaciones típicas |
Modbus | Media | Hasta 1.200 m | Sensores básicos, control local |
Profinet | Muy alta (Ethernet) | Hasta 100 m por nodo | Líneas de producción avanzadas |
Ethernet/IP | Muy alta | Hasta 100 m por nodo | Supervisión remota, sistemas SCADA |
CAN | Alta | Hasta 40 m a máxima velocidad | Automoción, maquinaria industrial |
Profibus | Media-alta | Hasta 1.200 m | Control de procesos, robótica |
Importancia de los buses de comunicación
Sincronización del sistema:
- Los buses garantizan que todos los módulos del PLC trabajen en armonía.
Conexión de múltiples dispositivos:
- Permiten que sensores, actuadores y otros PLCs se integren en un sistema cohesivo.
Optimización de procesos:
- Un bus eficiente reduce los tiempos de respuesta y mejora la productividad.
Interoperabilidad:
- Gracias a estándares como Profinet y Ethernet/IP, los buses permiten que dispositivos de diferentes fabricantes trabajen juntos.
Interfaces de comunicación: conectividad en la era moderna

Las interfaces de comunicación permiten conectar el PLC con otros dispositivos y sistemas, mejorando su funcionalidad y supervisión.
Protocolos comunes:
- Modbus: Amplio uso en la industria.
- Profinet: Ideal para entornos Ethernet industriales.
- Ethernet/IP: Alta capacidad para redes amplias.
Aplicaciones:
- Conexión con sistemas SCADA.
- Supervisión remota y diagnóstico.
- Intercambio de datos entre PLCs.
Unidad de programación: diseñando la inteligencia del PLC
La unidad de programación es la herramienta que permite al usuario crear y modificar los programas que ejecutará el PLC.
Herramientas:
- Hardware dedicado: Consolas específicas para programar PLCs.
- Software para PC: Aplicaciones como Step 7 o RSLogix 5000.
Lenguajes de programación comunes:
- Ladder (LD): Basado en diagramas eléctricos.
- Texto estructurado (ST): Similar a lenguajes como Pascal.
- Diagrama de bloques funcionales (FBD): Usa bloques gráficos.
¿Estás listo para optimizar tus sistemas con la mejor tecnología de autómatas?
En BAMA Sistemas, somos expertos en automatización industrial y programación de autómatas programables (PLCs) . Con nuestra experiencia y soluciones personalizadas, llevamos tus procesos al siguiente nivel, garantizando eficiencia, precisión y resultados sostenibles.
No dejes que tu industria se quede atrás.
Contáctanos hoy mismo y descubre cómo transformar tu producción con tecnología de vanguardia.
FAQ Sobre las partes de un PLC
1. ¿Qué puedo hacer si mi PLC empieza a fallar y no sé exactamente cuál es la causa?
Cuando un PLC empieza a fallar y no queda claro qué componente está dando problemas, lo más sensato es recurrir a un diagnóstico técnico. A menudo, el fallo no está en el autómata completo, sino en una parte concreta como los módulos de entrada/salida o la fuente de alimentación. Contar con un servicio especializado puede ayudarte a resolverlo sin tener que reemplazar el equipo entero.
2. ¿Siempre hay que cambiar las piezas que fallan en un PLC o se pueden reparar?
Cuando un PLC empieza a fallar y no queda claro qué componente está dando problemas, lo más sensato es recurrir a un diagnóstico técnico. A menudo, el fallo no está en el autómata completo, sino en una parte concreta como los módulos de entrada/salida o la fuente de alimentación. Contar con un servicio especializado puede ayudarte a resolverlo sin tener que reemplazar el equipo entero.
3. ¿Cada cuánto conviene revisar las partes de un PLC para evitar problemas?
Cuando un PLC empieza a fallar y no queda claro qué componente está dando problemas, lo más sensato es recurrir a un diagnóstico técnico. A menudo, el fallo no está en el autómata completo, sino en una parte concreta como los módulos de entrada/salida o la fuente de alimentación. Contar con un servicio especializado puede ayudarte a resolverlo sin tener que reemplazar el equipo entero.
4. ¿Qué partes del PLC suelen fallar más a menudo con el tiempo?
Los módulos de entrada/salida y las fuentes de alimentación suelen ser los primeros en dar señales de desgaste, sobre todo si están expuestos a variaciones eléctricas o a mucha actividad. Revisarlos periódicamente es clave para evitar fallos inesperados.
5. ¿Un pequeño fallo en una parte del PLC puede parar toda una línea de producción?
Sí, y más veces de las que parece. Un fallo en la CPU, en el bus de comunicación o en una salida digital puede afectar a todo el proceso. Por eso es tan importante detectar los síntomas a tiempo y contar con apoyo técnico si ocurre algo fuera de lo normal.
6. ¿Tiene sentido externalizar el mantenimiento de los PLC?
Sí, especialmente cuando se busca evitar paradas inesperadas o fallos difíciles de detectar. Tener a alguien que conozca bien cómo funcionan estos sistemas te ahorra tiempo y preocupaciones, y te permite centrarte en la producción con más tranquilidad.
7. ¿Se puede mejorar el rendimiento de un PLC sin cambiar piezas?
Claro. A veces basta con hacer una limpieza a fondo, revisar conexiones, ajustar parámetros o actualizar el software. Un buen mantenimiento puede devolverle al equipo su mejor rendimiento sin necesidad de grandes inversiones.